Tariffs Create Challenges for the Building Materials Industry
Posted on April 30, 2025
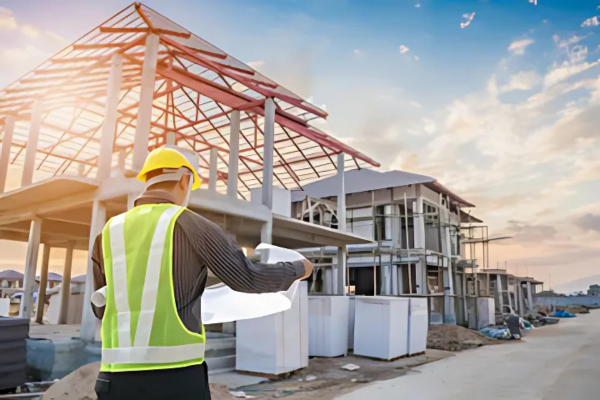
Tariffs on imported materials from countries like China, Canada, and Mexico drive construction costs and create challenges across the building materials and construction sectors. As the industry faces rising prices for essentials like steel, aluminum, and lumber, builders must adapt quickly to maintain project timelines and protect margins.
Rising Costs Hit the Construction Industry Hard
According to Moody’s Analytics via Construction.com, recent tariffs ranging from 10% to 25% have increased the cost of essential materials. These added expenses are affecting everything from single-family homes to large-scale infrastructure projects.
The National Association of Home Builders (NAHB) estimates that tariffs could add between $7,500 and $10,000 to the construction cost of a typical single-family home. This spike is particularly problematic as, according to Dodge Construction, the U.S. housing market is already struggling with a shortage of over 1.2 million units.
Lumber and Steel Supply Chain Challenges
A significant portion of U.S. construction relies on Canadian softwood lumber, which makes up 85% of lumber imports. Even though some exemptions exist, ConstructionDive reports that pricing pressures continue due to shifting trade policies. Some contractors have attempted to stockpile materials, but long-term planning remains difficult in this uncertain environment.
Nonresidential Construction Faces Investment Delays
The nonresidential sector hasn’t been spared. Material prices grew at an annualized rate of 9% in early 2025, based on findings from Daily Reporter. Rising costs have slowed private investment, as developers hesitate to move forward with projects amid financial unpredictability.
However, public infrastructure projects backed by the Infrastructure Investment and Jobs Act are helping sustain momentum in some regions, offering stability despite the volatility.
Labor Shortages Add to the Pressure
In addition to material costs, the construction industry faces a tight labor market. Stricter immigration policies and ongoing market disruptions have worsened labor shortages, further delaying project completion and increasing overhead.
What’s Next for the Building Materials Industry?
While some analysts suggest that tariffs may eventually boost domestic production, the short-term impact disproportionately affects small- and medium-sized businesses. These firms often lack the financial buffer to weather extended periods of inflated material and labor costs.
Key Takeaways:
-
Tariffs are raising prices on essential materials like steel, aluminum, and lumber.
-
Single-family home costs could increase by up to $10,000.
-
Canadian lumber remains vital but expensive despite some tariff exemptions.
-
Private construction investment is slowing, while public projects continue.
-
Labor shortages are compounding the impact of rising material costs.
Adaptability will be key as the building materials and construction industries navigate these shifting economic dynamics. To stay competitive in this evolving market, companies must rethink sourcing strategies, control costs wherever possible, and explore new ways to recruit skilled labor.